Stadium Series Ice Plant Rolls into Annapolis
The NHL officially took over Navy-Marine Corps Memorial Stadium to set the stage for Washington Capitals and Toronto Maple Leafs on March 3rd
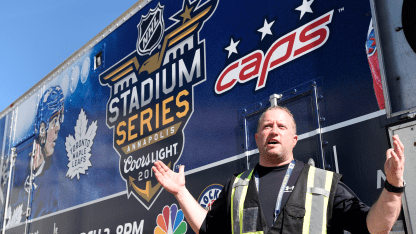
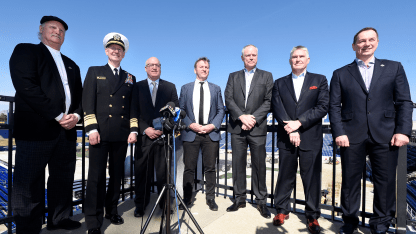
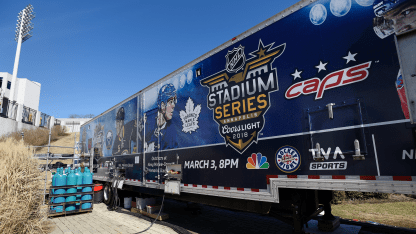
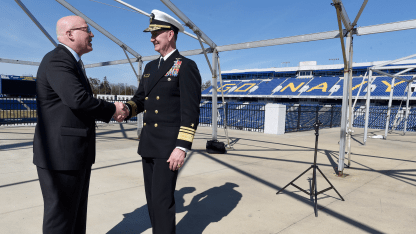
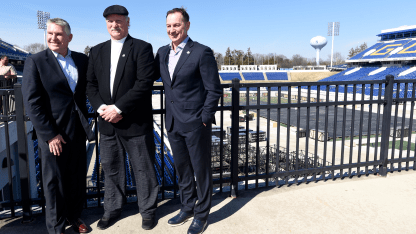
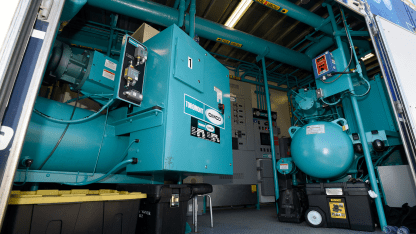
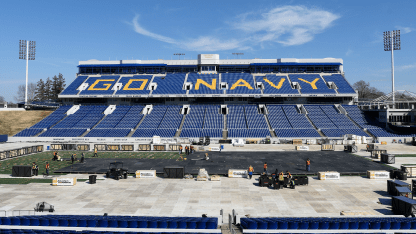
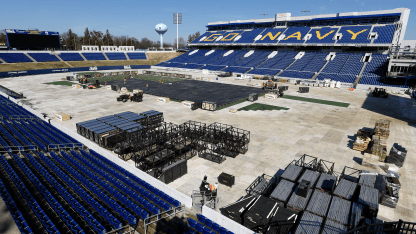
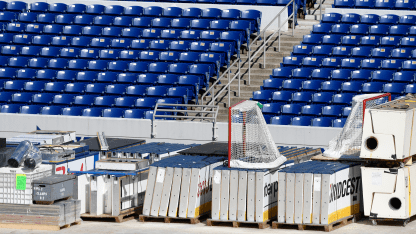
The NHL officially took over Navy-Marine Corps Memorial Stadium to set the stage for Washington Capitals and Toronto Maple Leafs on March 3rd