Over three days this past week, workers at the Kraken Training Center took three giant steps toward Seattle skaters stepping on the ice this fall. On Tuesday through Thursday, concrete was poured to form the bases for three NHL-regulation size rinks, 200 by 85 feet.
"We've been really busy the last six months trying to get a shell on this place," said Alex D'Avella, project manager for BNB Builders, which is the general contractor for the Northgate training center the Kraken and Pacific Northwest community will call home base for hockey, figure skating, power skating, public skating, curling, broomball, community events and lots more. "Getting windows in, siding, the roof. Seattle can get a little rainy [in the winter months]. Now, getting the ice slabs in."
Three's a Crowd-Pleaser
Skater alert: The Kraken Training Center's trio of ice rinks reached 'concrete' and significant milestones last week
KTC hits milestone with concrete ice slab pour
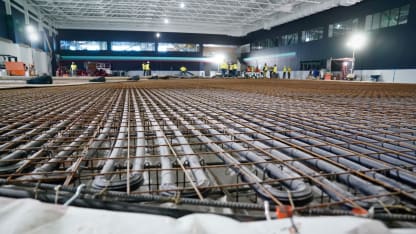